Around 80% of food manufacturers have reported an increase in productivity after implementing integrated quality management systems.
In the food industry, relying on paper-based quality systems can lead to significant inefficiencies, becoming more of a liability than a help. Picture this: you're rummaging through a mountain of paperwork just to find a single critical detail, or even worse, realizing that an essential document has been lost in the chaos. Mistakes in data entry, lost paperwork, and the delay in obtaining information can result in suboptimal decisions. Not to mention, manually tracking data eats up precious time and resources that could be better spent on mainline operations. Further complicating matters, maintaining compliance with food safety regulations becomes an uphill battle without immediate access to documents. These hurdles in productivity and efficiency signal a clear need for a shift towards integrated digital systems.
The use of digital systems can enhance transparency and visibility across the entire food production process.
Digital integration enhances operational efficiency by streamlining processes. It enables the automation of repetitive tasks, reducing the time spent on manual processes and freeing up resources for more strategic activities. This automation can lead to significant cost savings, as well as increased productivity and efficiency. For example, in the food industry, automated systems can monitor and control food production processes, ensuring consistent quality and reducing waste.
Another way digital integration enhances operational efficiency is through improved data management. Integrated systems provide a centralized platform for data collection, storage, and analysis. This allows for real-time visibility into operations, enabling quick decision-making and proactive problem-solving. In the context of the food industry, this could mean being able to identify and address issues in the supply chain before they become major problems, or making data-driven decisions about production schedules based on demand forecasts.Digital integration also promotes collaboration and communication across different departments and teams.
With integrated systems, information can be easily shared and accessed by all relevant parties, eliminating silos and fostering a more collaborative work environment. This can lead to better decision-making, as decisions are based on a holistic view of the organization's operations. In the food industry, this could mean better coordination between procurement, production, and distribution, leading to improved efficiency and quality control.Finally, digital integration supports continuous improvement, a key aspect of operational efficiency.
Integrated systems can provide valuable insights into performance, highlighting areas for improvement and enabling the tracking of progress over time. This allows organizations to continuously refine their processes and strategies, leading to ongoing efficiency gains.
In the food industry, this could mean using data to optimize recipes, improve packaging processes, or reduce energy consumption.
Overall, digital integration offers numerous benefits for operational efficiency, from process automation and improved data management to enhanced collaboration and continuous improvement.
By leveraging these benefits, organizations can drive efficiency, improve quality control, and ultimately, achieve their business objectives.
Here at Sensire, you'll find your one-stop shop for precisely that: Integrated digital systems that harness the power of automated condition monitoring, digital task management, and advanced analytics and reporting. But how does it all translate into operational efficiency and effective quality control in your food industry operations? Let's dig a little deeper.
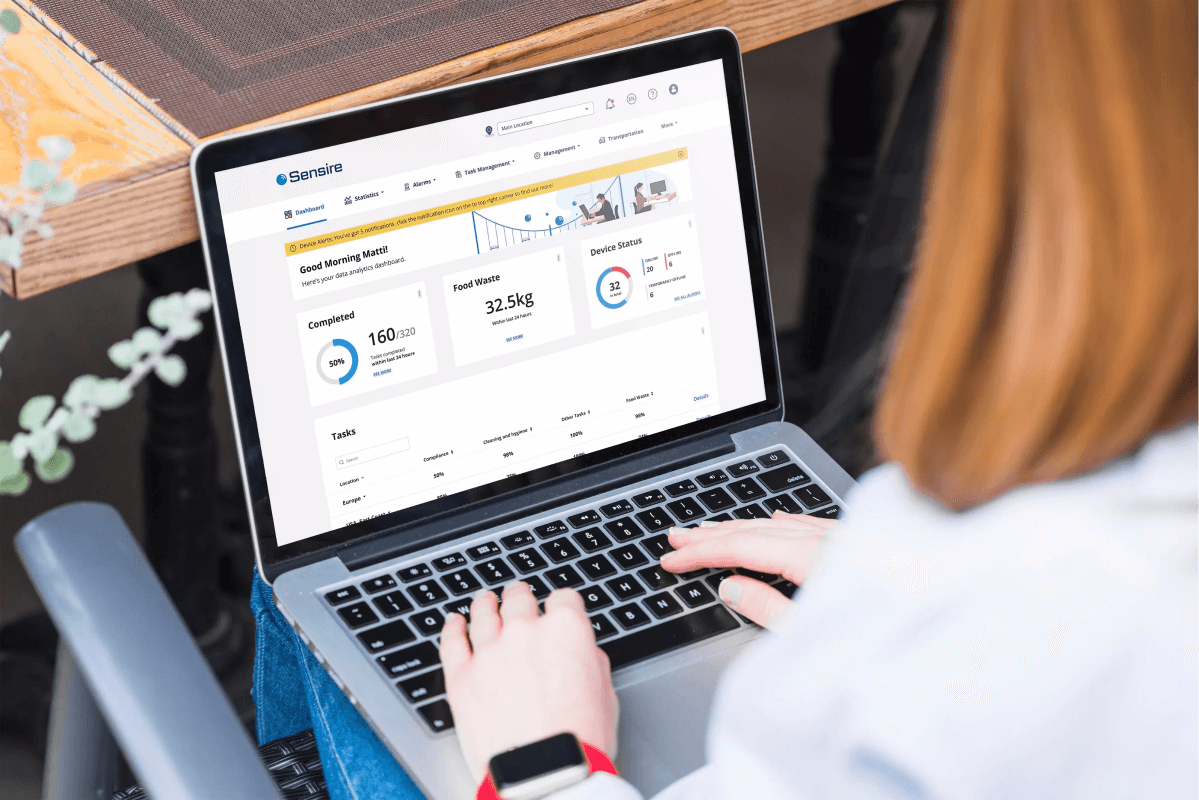
At the heart of our system is the automated condition monitoring. This powerful system continuously tracks the state of your production lines and identifies any abnormalities that could potentially disrupt operations. But it doesn't stop there. It also steps in to mitigate risks, sends alerts, and ensures your workflow remains unbroken. And, we do this across multiple locations, even countries. With Sensire, you get a globally consistent quality control system that never sleeps.
Incorporated into our systems is a uniquely designed digital task management tool. This tool streamlines work processes and eliminates the complexities of manual tracking. Tasks are assigned, progressed, and completed, all in real time, with an efficient digital handshake replacing the back-and-forth of traditional systems. The result is a noticeable increase in productivity, leaving more time for the critical tasks that drive your business forward.
The crown jewel, however, is our analytics and reporting function. Responsive, intuitive and adaptable, it brings together all the data from your operations — right down to each specific production line. It interprets this data, offering insightful reports that shape smarter decision-making, leading to enhanced quality control and operational efficiency.
So you see, your food industry operation's efficiency and quality control doesn't just improve with Sensire, it transforms. Our integrated digital systems adapt to serve your unique needs for just about every aspect of your operations, ensuring that no matter where you are, you're in total control.